Learn
How to Perform Electrical Maintenance
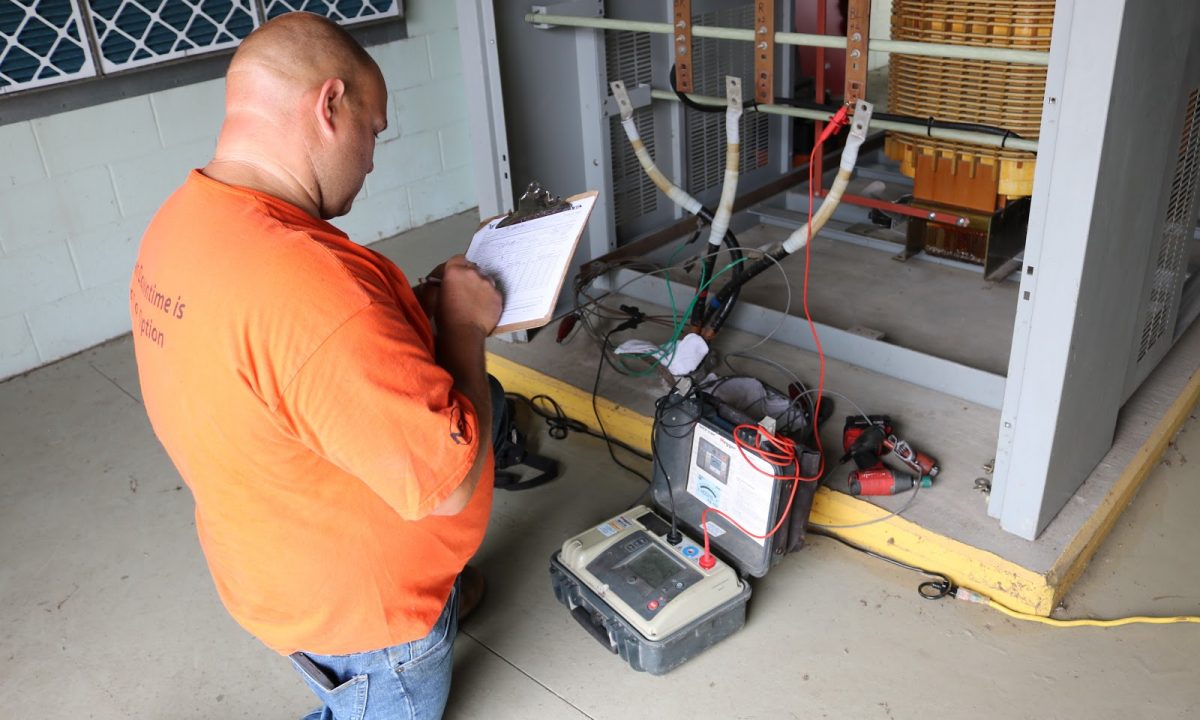
An electrical maintenance team or technician should perform electrical maintenance on all the key electrical apparatus that deliver power safely and reliably at a facility. It is done at places when downtime from power loss is not an option.
The following typically need inspection and/or testing:
- Switchgear and switchboard assemblies.
- Power and instrument transformers
- Cables
- Switches
- Circuit breakers
- Protective relays
- Metering devices
- Grounding systems
- Motor control centers
- Direct current systems/batteries
- Generators
- Emergency systems
- Auto transfer switches
- Control Panels
A qualified Technician uses the NETA/ANSI MTS-2019, or NFPA 70B standard to develop a complete Electrical Maintenance Program (EMP).
Here are the basic steps:
Step 1 – Make sure the one one-line drawing is current.
The first step in an electrical maintenance program is up-to-date one-line drawings. These are invaluable in electrical emergencies and building a rugged electrical maintenance program. “We are often called upon to service failed equipment that the client did not know belonged to them. They believed that the utility company owned the equipment. A validated one-line drawing would clear that up.” said Chris Halcomb, a NETA III Tech at Utilities Instrumentation Service.
Step 2 – Using current one-line drawings, create an inventory list of all electrical apparatus.
From the first electrical apparatus after the last utility company apparatus to the plant control panels, list all the electrical apparatus. This includes cables, backup batteries, and generators.
Step 3 – Assess the condition of the apparatus.
About one in three hundred breakers fail in the first three years, one in a thousand the following three years, after which the incident of failure rises again to one in 100 after 25 years. Statistics are similar for most electrical apparatus. Hence, electrical maintenance increases in frequency as the apparatus ages.
Another factor to consider in the maintenance frequency is the conditions around the electrical apparatus. A steel mill has an environment with heavy particulates collecting on insulating surfaces. These can track to the ground causing premature failures. On the other hand, hospitals are less vulnerable to such a failure.
Step 4 – Assess the operational and safety impact of the apparatus.
Some equipment might be operating the building cooling fans, while others are operating MRIs at hospitals or furnaces in a steel mill. Each electrical apparatus must be evaluated on its impact on operations and safety to determine the frequency of maintenance.
Step 5 – Develop a quality electrical preventative maintenance program. (EMP)
Once all five steps are done, the EMP table will look like table A below.
Table A
An electrical maintenance team or technician can then perform electrical maintenance on all the key electrical apparatus. Specific testing techniques for each type of equipment per the standards will be established. This could include “shooting hotspots” more properly called IR Scanning and “injecting electrons,” more properly called secondary injection of breakers. In the end, these efforts mitigate downtime and help suppress “artificial lightning” more properly called Arc Flash.
Learn more by downloading our Why, What, When, and Who of Electrical Maintenance white paper.