Learn
Employee overrode alarm 460 times before Huron River Spill – Can this happen to you?
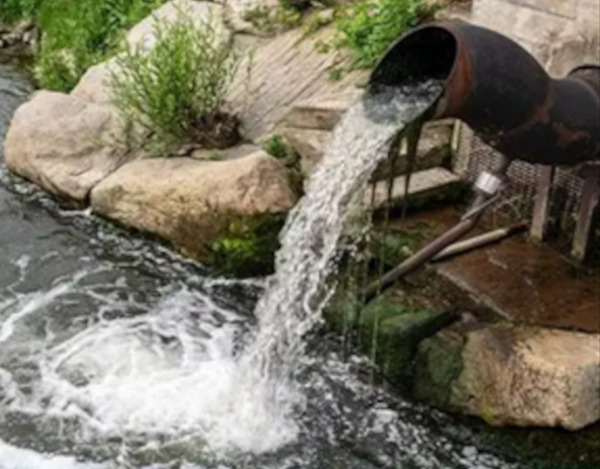
MLive reported in August 2022 that the Tribar plant operator in Wixom overrode an alarm 460 times in a span of three hours resulting in the overwhelming discharge of “acid etch material” to the Wixom wastewater plant that discharges to the Huron River. Tribar spent millions of dollars to have the technology to protect themselves and yet this happened.
It’s likely your municipality or plant has spent millions of dollars in technology to ensure that spills of contaminated water are not discharged back to nature. Or contaminated clean water is not delivered to residents. Yet, this event inevitably forces the industry to ask: “Could this happen to us?”.
How can you protect yourself? For plants that are properly designed for the contaminants that can be found in the influent, here is a best practice program that is recommended.
1 – Calibrate Instruments. Establish a calibration routine for critical and less critical instruments. The critical sensors are typically those used for billing
and/or regulatory purposes. These can be influent and effluent flow, pH, dissolved oxygen(DO), and oxygen reduction potential(ORP). The less critical sensors are those used in internal processes such as tank levels, chemical feed, pressure, and temperature. These sensors provide the input necessary to operate all processes and alarm when necessary. Based on a 2018 from UIS SCADA, it was found that 7 percent of tested instruments need repair and/or calibration. See the report below.
Click here for a paper on the Why, What, When, and Who of Municipal Calibration.
2 – Validate the telemetry. Once instruments are proven precise and accurate, a good instrument calibration tech will validate that the sensors are effectively communicating with the field device, such as a data logger, programmable logic controller (PLC), or programmable automation controller (PAC). In addition, they will confirm that the human-machine interface (HMI) is reporting the correct figures.
3 – Validate the process. The input signals are either digital (on or off) or analog (a range of signals). These are read by the field device, which response with outputs that can be digital such as turning something on or off, or analog, increasing or decreasing the amount or speed of something, or communicating an alarm. All these responses are part of a program. To validate that the program works regardless of input will require a programmer and plant operators working together to stress test, either live or virtually, all the system scenarios. This could include extreme conditions such as getting a 0 milliamp reading from a signal that should be between 4 to 20.
This is typically done at the start-up of a new system. However, the best practices are to do stress testing during calibration as well. This is something that is often overlooked at the time of calibration.
4 – Develop sound Alarm Management. Alarm management standards for your plant can be developed using the ANSI/ISA 18.2 Alarm Management Standard. OSHA acknowledges this standard as “Recognized and Generally accepted good engineering practices.”
Some key parts of a good alarm management system are:
- Don’t cry wolf. The alarm management must differentiate alarms that require immediate attention from those that are informative. Otherwise, it can cause alarm apathy.
- The alarm must go to “need to know” personnel only. Sending alarms to operators that have no responsibility again leads to alarm apathy. However, escalating the alarms if there is no acknowledgment is highly recommended.
- Program out cascading alarms. For example, if power is lost at the head end, you may get communication failure alarms as well.
- Time limit Alarms Suppression when doing maintenance. It is typical to get many alarms while doing maintenance. Design the program to deactivate those alarms for a set time to avoid alarm apathy and the risk of not re-activating the alarms after maintenance is completed.
- Prioritize alarms. Some alarms require immediate attention, while others are more needed to trigger a work order.
- Avoid “Acknowledge All.” The risk is that buried in those alarms is one that is missed.
- Manage Logins. Each operator must have their own login. This holds each individual accountable. And delete logins when the employee leaves the organization to avoid the risk of damage done by a disgruntled employee.
Some examples of red vs. yellow alarms see the two tables below.
In sum, operating a critical process like a wastewater or water plant is a serious business. Following best practices provides peace of mind that your plant will consistently deliver clean water. If you are not sure how to get started in these four steps, give our experts a call at 734-787-6410.