Learn
Avoid downtime with Electrical Maintenance
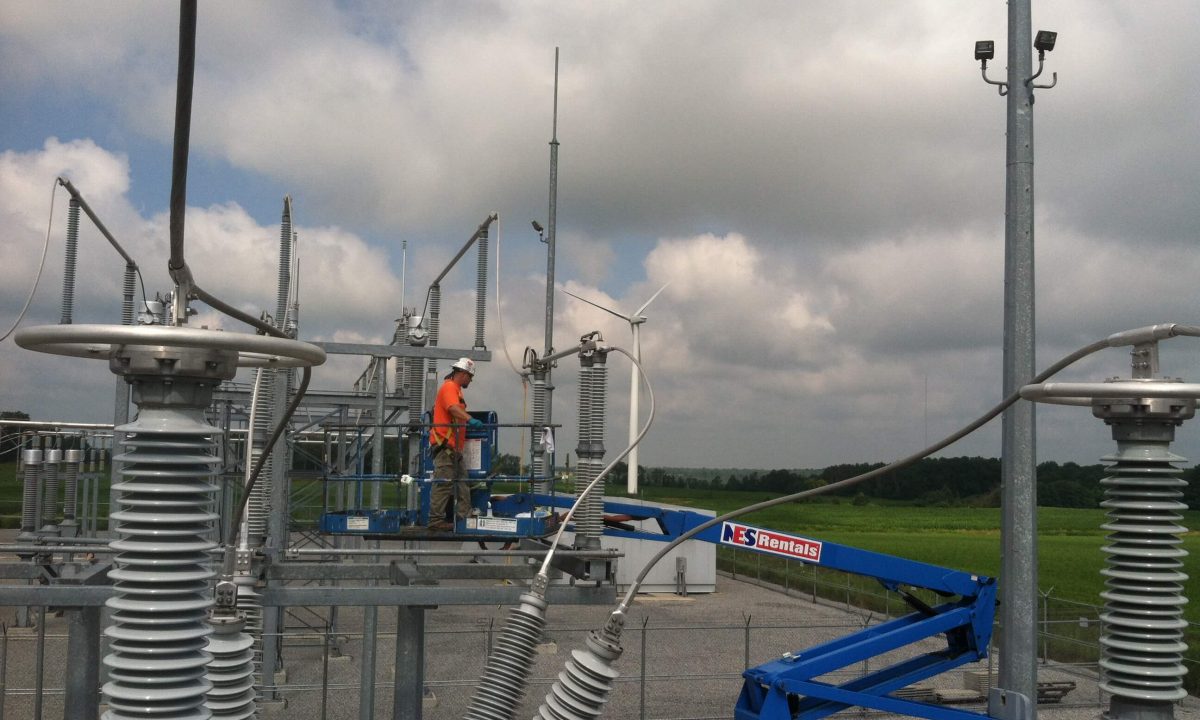
What is the cost of losing power for one hour at your facility?
Or a shift?
Or 24 hours?
These are questions you should be asking yourself if you are in charge of the electrical maintenance of your facility or organization. If you work in an organization where downtime is not an option, then electrical maintenance plays an essential part in avoiding costly shutdowns. Working in organizations such as hospitals, manufacturing, and automotive plants, water and wastewater plants, universities and colleges, commercial buildings, data centers, airports, and power generating facilities such as carbon-based, wind, solar, and hydro. You need a professional organization that can keep power and controls safe and reliable.
When was your equipment last inspected or maintained?
Professional organizations can help you create and keep your electrical equipment maintenance plan optimized for you. As soon as new equipment is installed, a process of normal deterioration begins. If left unchecked, the deterioration process can cause malfunction or an electrical failure. Electrical equipment life can be extended dramatically by simple precautions that promote:
- Cleanliness
- Dryness
- Tightness
- Prevention of friction
These facilities have complex electrical systems with switchgear, control panels, motor control centers, and other electrical apparatus that have the potential to shut down facilities or expose people to serious workplace hazards.
Does it protect your staff?
According to two studies, 1 in 200 transformers and 1 in 100 breakers fail every year. In addition, The ElectricalSafety Foundation International reported that in 2018 there were 160 electrical deaths and 1,560 electrical injuries. Most of these catastrophes can be avoided by taking the necessary steps to mitigate downtime.
There are three reasons to do electrical maintenance:
1. Safety
2. Reliability
3. Insurance
Safety
The safety hazards can be electrical shock, electrocution, burns, fire, and powerful explosions that can blow the door off a panel. The two tables below show the latest US statistics and are courtesy of the Electrical Safety Foundation International. Electrical maintenance and enhanced safety practices have had a significant impact on reducing fatalities and injuries.
Reliability
Common examples of the causes of unexpected failures are mechanical failures, water, ice, wind, accumulation of dirt, corrosion, mice, raccoons, vegetation, insects, spider webs, electrical component failure, and even forgotten tools. Some examples of real downtime are a large hotel out of power for a few days due to a failed transformer by tracking from dirt; a section of a manufacturing facility closed due to an exploded breaker, again by dirt tracking to ground; and an airport shut down from water damage and corrosion in the electrical system. There is limited data on the failure rate of common electrical system components.
What is driving up the safety and reliability of electrical systems? It is the push to implement good maintenance and operating practices defined by the NFPA-70B-2019 Recommended Practice for the Electrical Equipment Maintenance, NFPA 70E Standard for Electrical Safety in the Workplace, and the ANSI NETA MTS-2019 Standard for Maintenance Testing Specifications for electrical power equipment and systems.
Insurance
Key findings have shown, “62 percent of equipment breakdown losses were due to lack of maintenance, accounting for three-quarters of all equipment loss claims paid.” Download our 4 w’s of Electrical Maintenance white paper to read more about the importance of Electrical Maintenance.