Learn
How to Upgrade SCADA: The MHOG Story
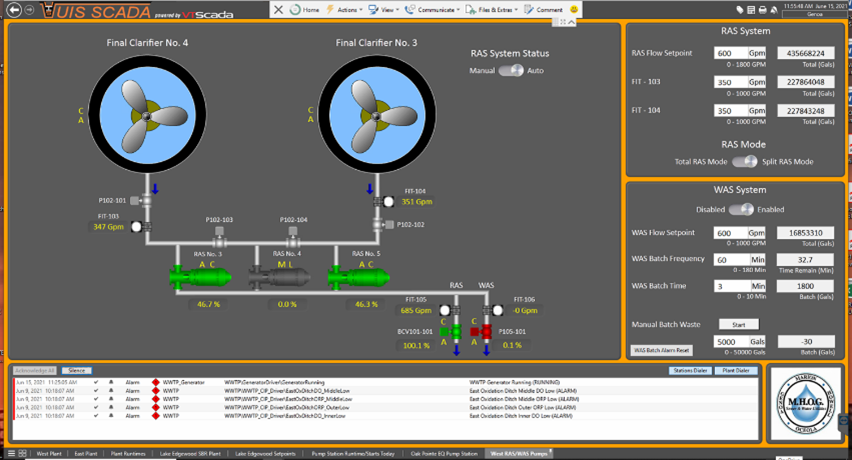
79% of US municipalities have a SCADA system, and of those who don’t, 80% were in the process of implementing SCADA in 2018. This is the most current data available in a 2018 AWWA State of the Water Industry Report. Hence, most municipalities understand what SCADA can do and are making their future investments in SCADA project upgrades.
MHOG Story
The MHOG Utility Department serves four townships in Michigan: Marion, Howell, Oceola, and Genoa. They had an old SCADA system that needed an upgrade and did not use the low-bid procurement process. Instead, they used a process that loosely follows the Qualficatication-Based Selection (QBS) procurement process.
The first step was to document their critical SCADA needs where the scope of work, list of assets, parameters, and key SCADA features are listed. This included a description of the operational concept and sketches of the SCADA screen they wanted. See the two diagrams below.
MHOG’s Critical SCADA Needs List
- Remote Monitoring and Control
- Customizable to MHOG’s Utility
- Adaptable to expansion, process changes, and maintenance projects (Example: New process online, Water tower out of service)
- Prompt Alarm Notification and alarm history
- Remote access anytime and anywhere
- Data Tracking
- Real-time and historical data for trending, process analysis, and demand analysis
- Data for regulatory compliance: ie. – Asset Management Reporting, reliable studies, risk and resiliency analysis
- Interactable dashboard schematically related to actual field conditions
- Reporting connected to EGLE monthly operating report requirements
- User-friendly and intuitive for operations staff, yet secure from outside dangers
- easily implement alarm conditions and parameter changes
- Historic vs. real-time data analysis
After generating all the necessary preliminary documents, they selected UIS SCADA, their current SCADA integrator. Together they refined the scope of work and negotiated a fee.
Easy Conversion of Sketches to Working SCADA Screen
The integrator took the sketches and converted them into a SCADA screen. See the two diagrams below.
Designed in a Tower-out-of-Service Capability
MHOG added to the scope the ability to maintain water pressure with the water tower out of service. In addition, the design eliminated the need for high pressure blow off relief valves and pressure-reducing valves or pressure-sustaining valves. They used a variable speed drive driven by a mathematical formula to maintain the target pressure to deliver the desired pressure and volume. The whole process was part of the SCADA system, where it was easily interfaced by the operators. Below is the screen they developed and the performance curve when they took the tower out of service.
Benefits Observed
- Improved operational maintenance: SCADA tracks the data, giving MHOG operators the ability to see the problems before catastrophic conditions occur. Examples are the ragging of pumps, water system demand trends, and check valve clogging.
- Reduced overtime cost: Operators can securely and remotely interact with the system on their phones. This gives them the ability to determine if a physical response is required, make changes remotely, and perform manual operations, such as the manual iron filter backwash during high demand, remotely.
- Enhanced operator support and skill: The development of the scope of work and project implementation was done with significant input from the operators resulting in a high level of buy-in and operational skill.
- Employee accountability: Management can see who acknowledged the alarm and the full call. In addition, the SCADA system can be programmed to deliver emails and text messages to provide added security for alarms and event responses, thus reducing the risk of missing an alarm.
In sum, if your team already understands how SCADA works, using a Qualified-Based-Selection versus a Low-Bid procurement process delivers the best value.
A 2009 study by Paul S. Chinowski, PhD., University of Colorado and Gordon A. Kingsley, PhD., Georgia Institute of Technology (2009), “An Analysis of Issues Pertaining to Qualifications-Based Selection,” found that QBS:
- Reduces change order costs from 10% of the overall project to 3%
- Lowers risk for complex projects
- Shows that 93% of owners surveyed on QBS projects in the study rated the success as high or very high
- Includes more stakeholders in the design process
- Promotes a high level of innovation
- Enhances the future municipal operating staff’s capability
Maximize post-sales service, quality, and value – hire the best with QBS.