Learn
Difference between RTU and PLC
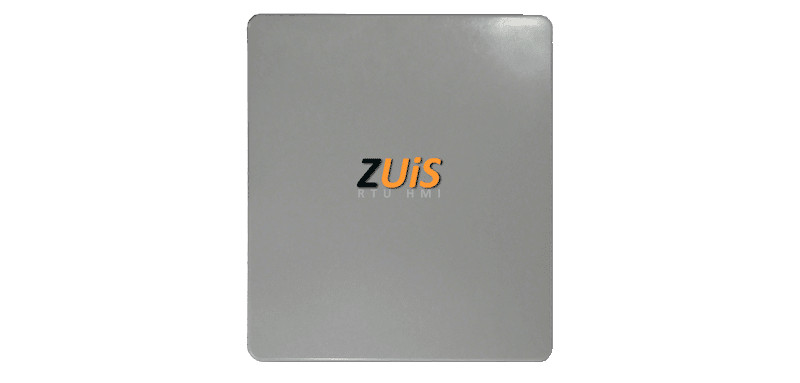
There are many RTUs and PLCs currently on the market. Advances in both classes are increasingly blurring the line between them. Yet, some key differences remain. What are the differences between RTU and PLC? Knowing the differences and functionality of both can help you make the right decision for your facility.
The Basics
RTU – (Remote Terminal Unit):
On the most superficial, simple level, RTUs are designed for remote monitoring and control stations. They are typically found where communication requires radio, cell, or other forms of long-distance communication and where weather conditions are extreme. Since they are located in remote sites, they are more vulnerable to unauthorized access; hence, they need a higher level of physical, telemetry, and cybersecurity as well. They are typically found in oil well pumping sites, power substations, and water and wastewater networks.
The focus of RTU is on remote monitoring with control, but with a higher demand for application communications and protocol flexibility. Therefore, these designs tend to be greater in CPU horsepower, programming flexibility, and broader communication support than PLC systems. There are several critical areas to consider.
- Rugged and reliable hardware constructions
- Extensive programming and performance capabilities
- Broad communication and protocol support
- Local Control horsepower
- Remote programming and downloads
- Scalability of Security
- Stronger-edge computer power
PLC- (Programmable Logic Controllers):
On the simplest level, PLCs are primarily designed for local monitoring and control. They are typically found where there is no need for remote communication or where communication is via ethernet, Wi-Fi, or fiber optics inside the same building. They don’t require the same level of weather resistance, the multitude of communication protocols, or security.
PLC’s purpose was initially designed to replace relay logic. PLCs acquire analog and/or digital data through input modules and execute a program loop while scanning the inputs and taking actions based on these inputs. PLC’s performance excels when there are sequential logic control applications with high discrete I/O data counts. These are the factors to consider for selecting a PLC:
- I/O requirements
- Type of communication protocols
- Remote communication options
- Processor speed
- Programming language
PLCs are not equal to RTUs
Because of these differences, a poor selection will lead to wasting dollars, missing necessary capabilities, shorter operating life, or security breaches. When it comes to what information you (as a facility manager) want to know in order to make a sound decision, we suggested starting with the following:
Know before you press go:
- Current and future I/O and process requirements
- Communication and protocol requirements for your changing sensors
- Local vs. remote intelligence and processing
- Ease of remote programming and downloads
- Temperature, humidity, and vibration resistance requirements
- Mechanical, Cyber, and Telemetry security needs
Table showing the differences.
Product recommendations
UIS SCADA values doing the job the first time with highly reliable PLCs and RTUs. Hence, before they agree to use new equipment in their jobs, they vet the organization and equipment to ensure a reliable start-up and years of performance. They delivered to their clients and trusted electrical contractors top-of-the-line quality equipment and SCADA systems with 20+ years of trouble-free performance.
If you’re not sure how to proceed, contact our field techs, who will recommend the appropriate unit based on your facility’s requirements and budget. Here are some examples of units UIS SCADA chooses to use.
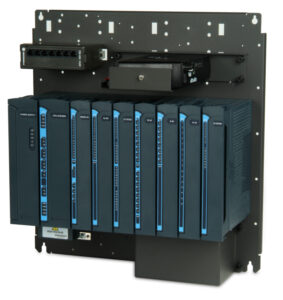
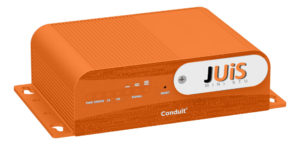
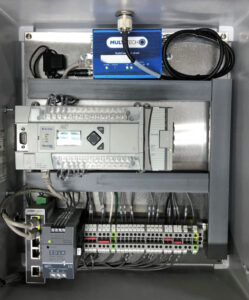
Learn More
To learn more in-depth about what unit best suits your facility’s needs, please download our white paper: RTU vs. PLC or our literature on our ZUiS M RTU, and ZUiS A PLC.