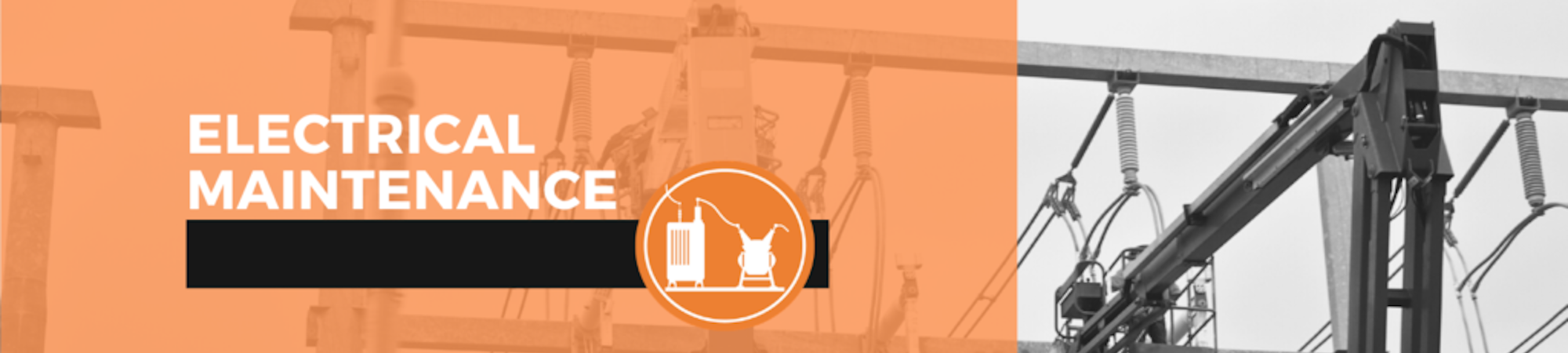
Acceptance and Maintenance Testing
In 1970s, it was recognized that the rapid growth of increasingly complex electrical systems demanded oversight to promote safety and system reliability. In 1972, organizations came together to create NETA as well as the first standard, Acceptance Testing Specifications for Electrical Power Equipment and Systems. In 1975, the NETA Electrical Testing Technician Certification was established. Today, NETA has grown beyond the United States. Its standard has become ANSI Accredited and is the gold standard for all firms that perform Electrical Acceptance and Maintenance Testing.
Today, there are three standards for electrical acceptance and maintenance testing, sometimes called power testing or high voltage testing :
- NFPA-70B-2023 Recommended Practice for the Electrical Equipment Maintenance
- ANSI/NETA MTS-2023 Standard for Maintenance Testing Specifications for electrical power equipment
- ANSI/NETA ATA-2021, Acceptance Testing Specifications for electrical power equipment and systems.
NFPA-70B-2023 Recommended Practice for the Electrical Equipment Maintenance
Maintenance intervals are no longer just a suggestion. Chapter 9 of NFPA 70B 2023 Edition sets the stage for mandatory scopes of work and maintenance intervals tailored to your equipment type and condition. These intervals are your compass, guiding you through the journey ahead. Check out our NFPA 70B article to learn more.
Electrical Acceptance Testing Specifications
Acceptance testing is done after the installation of a new electrical system and before energizing. The ANSI/NETA Acceptance Testing Specifications provide detailed instructions to assure that the tested electrical equipment and systems are operational, within applicable standards and manufacturer’s tolerances, and installed in accordance with design specifications. This website covers most of the services that are available in acceptance testing.
Electrical Maintenance Testing Specifications
All electrical systems degrade over time from corrosion, gelling of lubricants, heat, moisture, insects, animals, airborne dirt, and other foreign contaminants. If maintenance is not performed, electrical failure is inevitable. It will likely cause unexpected downtime and raise the risk of an electrical injury or fatality. The ANSI/NETA Maintenance Testing Specifications helps facility manager develop the right electrical maintenance plan (EMP). A good EMP balances the cost of electrical failure and electrical maintenance. This website covers most of the services that are available in maintenance testing.
A good EMP program includes the following:
- Up-to-date one-line drawing of the electrical system
- Complete list of electrical equipment, their condition, and their impact on safety and operational reliability
- Testing schedule using ANSI/NETA Testing and Maintenance standards
- Execution of the routine electrical testing by qualified personnel
- Post Testing reports with recommended electrical maintenance and deficiencies that outline proper corrective measures can be prescribed