Learn
Why Do Calibrations?
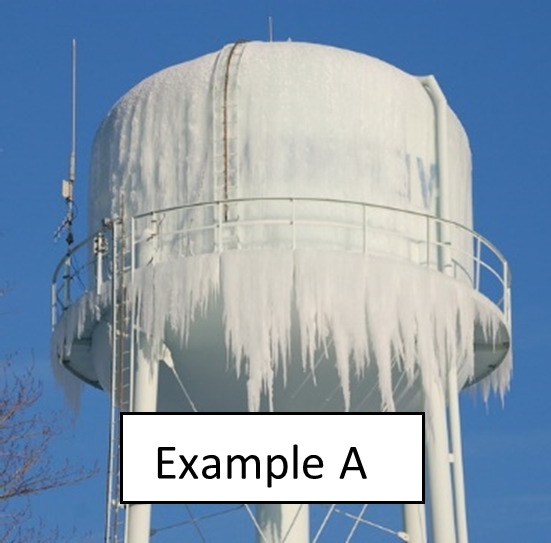
Calibrations are fundamental to building the public’s trust in almost everything purchased today. Most products, such as water, cars, fuel, electricity, and many more, depend on accurate measurements. Accurate measurements are only possible if the instruments reporting the measurements are routinely calibrated. A world without calibrations would degrade trust through poor-quality products, giving room for a feeling of being cheated when what is provided is less than expected. When it comes to facility calibrations being accurate, there are higher safety concerns. Calibrations quietly maintain order in the things we have come to depend on.
A summary of reasons to do calibrations are as follows:
- Meet code requirements and avoid legal penalties – As mentioned above, codes require proper operation and maintenance. Doing instrument calibrations on a periodic basis is the industry best practice and constitutes proper maintenance. This is part of the maintenance that will help facilities and operators avoid legal penalties.
- Reporting – As mentioned above, keeping records of proper operations and maintenance for agencies such as the EPA and EGLE is required by code. Part of that is a record of periodic calibrations to ensure that reported figures are accurate.
- Good maintenance practice – OEM Equipment and Instrument Manuals recommend periodic inspections and calibration frequencies as part of the maintenance program. This includes cycling all the components, such as valves and gates, that normally do not get cycled. Checking for residue build-up, leaks, and build-up from leaks at connections, instrument logs for errors, clearing logs as needed, and reviewing past calibration documentation to compare current readings to past readings.
- Asset management – Help plan infrastructure upgrades.
- Process performance – Optimize processes such as chemical feed and DO blowers
- Test alarms – Simulate alarm conditions to ensure all parts of the SCADA system, such as the instrument, the field device, the telemetry, the SCADA software, and the operator response, work perfectly.
Periodic Calibration Is a Best Practice for Instrument Maintenance
Like gas pumps, wear and tear of mechanical and electronic components of water and wastewater instruments diminish accuracy. In 2022, UIS calibrated 3,204 instruments, and 5.3% were out of calibration or defective. See the historical table below.
Since most calibrations are done annually, after one year, on average, 1 out of 20 instruments does not report accurately. How many instruments are in your plant? When was the last time calibrations were done, and were they properly documented?
Why Calibrate?
Whether you work in water or wastewater, you are part of a team responsible for the safe and reliable delivery of clean water. If your facility is like most water and wastewater facilities, regulatory demands are rising, staff levels are diminishing, systems are getting more complex, and your most experienced staff is either retiring or close to retiring. In addition, unlike manufacturing, chemical, or other process-driven businesses, you cannot stop the process for a holiday or a weekend. You and your team can not work 24 hours a day. Therefore, you need the means to know how the system always performs and when the wheels start to get wobbly or fall off. To make that possible, you need a reliable data feed of your control systems. That is only possible if instruments are routinely calibrated and maintained. A good calibration program assures these and prevents other costly emergencies, repair costs, and regulatory infractions.
Summary
Calibrations are vital to maintaining trust with your residents, avoiding regulatory penalties, and running an efficient process.
Learn More
For a deeper dive into this topic, download our white paper: Calibration Builds Trust