Learn
Have You Scheduled Your Transformer Oil Test?
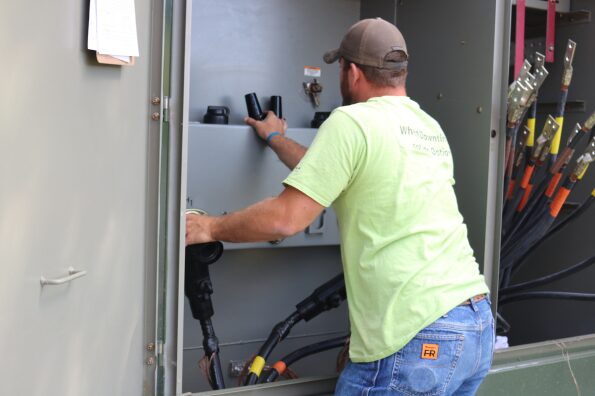
The health of your electrical equipment relies on regularly scheduled maintenance.
Transformer Oil Tests
Power-dependent municipalities, industrial manufacturers, data centers, and more industries should know the importance of regularly scheduled transformer oil tests. These industries are laser-focused on always remaining fully operational. When downtime from power loss is not an option. Transformers are a vital component of reliability. Transformer oil tests provide several purposes supporting this task, including insulation and cooling. As the oil in this equipment degrades, its capacity diminishes. To this end, transformer oil tests via sample as part of a regularly scheduled maintenance routine ensures optimal oil quality that extends the operation life of the electrical system.
Industrial transformer applications are a vital component of reliability, as their breakdown results in a loss of power, rendering an entire business, city or state without power. Regular maintenance and inspections, including taking oil samples for analysis can indicate that there is a risk of large-scale power failures or safety accidents due to poor oil quality. With the proper care, it’s possible to maximize the operation of your equipment, avoid any catastrophic failures and save money as well.
Case Study: Leaking Transformer Causes Big Problems
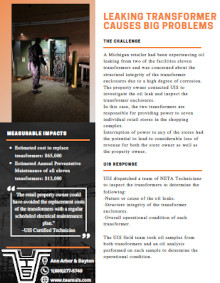
What is Transformer Oil Analysis?
Transformer oil analysis enables the diagnosis of any potential issues that lead to transformer failure. This type of testing reveals changes in the acidity and water composition of the oil, both of which can lead to partial or total electrical discharges. These include overheating, arcing, partial discharge, contamination, degradation and aging. Based on the results, any number of actions can be taken to improve oil quality.
Comprehensive testing considers many aspects of oil quality, including:
Visual analysis:
Assesses the appearance of the oil in terms of clarity, color, and the observation of foreign particles or cloudiness. Healthy oil is clear, transparent and free from contamination or deterioration.
Dielectric breakdown voltage (BDV) testing:
When two electrodes are immersed in oil, then subject to a gradual voltage increase until the oil fails electrically to determine oil performance under electric stress.
Color analysis:
Compares the color of a current oil sample against a previous sample to determine the degree of oxidation or contamination, as indicated by darkening of the oil over time.
Dissolved gas analysis (DGA):
This considers gases dissolved in an oil sample. Testing is done using chromatography or spectroscopy techniques for detection and identification of gases typically generated by faults or degradation in the transformer. Dissolved metals tests use atomic absorption or emission spectroscopy techniques to detect and quantify the nature and level of metals, including corrosion products or wear particles in the oil that can be a potential source of contamination.
During flashpoint or fire point testing:
The oil temperature is measured during heating to determine the temperature it ignites or sustains combustion to identify the presence of volatile or flammable contaminants in the oil including fuel, solvent or moisture.
Furanic compound testing:
involves the detection and quantification of furanic compounds formed by cellulose insulation material degradation within an oil sample. It relies on high-performance liquid chromatography techniques (HPLC) to the degree of degradation, as indicated by a high level of furanic compound content. Interfacial tension tests measure the force required to break any thin films in contact with water to determine the presences of polar contamination or oxidation products. Poor oil quality is a function of lower interfacial tension.
When to Test
How often should maintenance occur? Routine sampling as a regularly scheduled maintenance should happen at least once a year to ensure operational reliability and efficiency of electrical equipment. However, testing frequency often depends on the size and type of transformer as well as suggested maintenance per the manufacturer, industry regulations, the age and condition of the oil itself, and the operating environment. Our NETA certified technicians will know what the proper maintenance schedule is per your equipment.
Still other events may warrant testing, including equipment installation, during repair work, any changes in operating conditions, evidence of oil degradation and as a means of verification or troubleshooting. All must be completed using highly specialized equipment according to industry standards as set forth by the American Society for Testing and Materials (ASTM), a nonprofit organization that publishes thousands of technical standards for testing and classification of materials.
Need Guidance on Testing? UIS Has the Experts, and Expertise to Help
Identifying what is required for your maintenance needs, including the required standards for your applications, plus obtaining the right equipment to execute proper testing is often a daunting, time-consuming and expensive task for most municipalities and local businesses.
Not sure where to start, exactly? Utilities Instrumentation Service (UIS) is a NETA company with the experience and the expertise to help. UIS is a niche company that specializes in electrical testing and maintenance on a variety of equipment, including substations, transformers and breakers. UIS experts can help you stay ahead of any events resulting in failure to help keep the power flowing, without interruption.
From your initial contact, you’ll be put in touch with experts, rather than salespeople who understand the ins and outs of transformer oil testing. Based on a schematic of the facility involved, Team UIS experts can review your situation, and conduct an interview over the phone to identify any potential issues, then make a testing plan to stay ahead of them.
Tests of fluid quality should be standard practice for circuit breaker maintenance. Leave your testing up to the experts at UIS to avoid false readings that lead to contamination and equipment failure.
Reference materials consulted: Transformer Oil Sampling: A Guide to Best Practices | Electrical4U; Transformer Oil Testing: Types, Methods and Analysis of Insulating Oil (With Quiz) (engineeringworldchannel.com); ASTM International (ansi.org)